Porosity in Welding: Identifying Common Issues and Implementing Ideal Practices for Avoidance
Porosity in welding is a pervasive problem that often goes unnoticed till it causes considerable issues with the honesty of welds. This common problem can jeopardize the stamina and toughness of welded structures, posturing security risks and leading to expensive rework. By comprehending the root triggers of porosity and executing reliable prevention strategies, welders can dramatically enhance the quality and integrity of their welds. In this discussion, we will certainly check out the vital aspects contributing to porosity development, analyze its damaging impacts on weld performance, and go over the very best techniques that can be taken on to reduce porosity event in welding processes.
Typical Sources Of Porosity
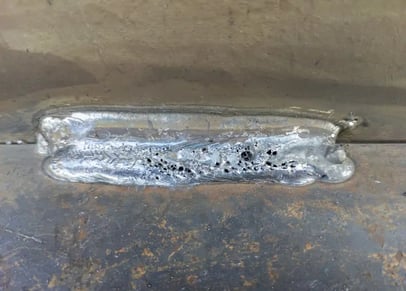
An additional frequent culprit behind porosity is the presence of pollutants externally of the base steel, such as oil, grease, or rust. When these pollutants are not successfully eliminated before welding, they can vaporize and become trapped in the weld, causing defects. Using dirty or damp filler products can introduce impurities into the weld, adding to porosity problems. To reduce these common reasons for porosity, comprehensive cleansing of base steels, appropriate shielding gas option, and adherence to optimum welding specifications are vital practices in attaining high-grade, porosity-free welds.
Effect of Porosity on Weld Quality

The visibility of porosity in welding can significantly jeopardize the architectural honesty and mechanical homes of bonded joints. Porosity develops voids within the weld metal, compromising its general toughness and load-bearing ability.
Welds with high porosity levels tend to show reduced effect strength and reduced ability to flaw plastically prior to fracturing. Porosity can hamper the weld's ability to effectively transmit pressures, leading to premature weld failure and possible safety and security dangers in vital structures.
Ideal Practices for Porosity Avoidance
To improve the architectural honesty and quality of welded joints, what particular procedures can be applied to minimize the occurrence of porosity during the welding process? Utilizing the right welding strategy for the details material being welded, such as adjusting the welding angle and gun setting, can additionally stop porosity. Normal Discover More Here examination of welds and prompt removal of any kind of concerns recognized throughout the welding procedure are essential practices to avoid porosity and produce premium welds.
Value of Appropriate Welding Methods
Executing appropriate his comment is here welding techniques is critical in guaranteeing the structural integrity and high quality of bonded joints, building on the structure of efficient porosity prevention measures. Welding strategies straight affect the general strength and resilience of the welded framework. One crucial element of proper welding strategies is maintaining the appropriate heat input. Excessive warmth can cause enhanced porosity due to the entrapment of gases in the weld swimming pool. Alternatively, inadequate heat might lead to incomplete fusion, developing prospective weak points in the joint. In addition, utilizing the suitable welding criteria, such as voltage, present, and travel rate, is essential for attaining sound welds with minimal porosity.
Additionally, the selection of welding procedure, whether it be MIG, TIG, or stick welding, need to align with the specific demands of the task to guarantee ideal outcomes. Proper cleaning and prep work of the base steel, as well as choosing the appropriate filler product, are also vital parts of competent welding methods. By sticking to these ideal practices, welders can reduce the danger of porosity development and generate top quality, structurally sound welds.
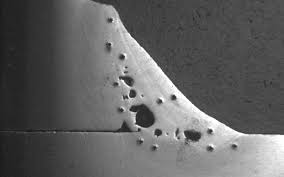
Testing and High Quality Control Actions
Testing treatments are essential to spot and prevent porosity in welding, guaranteeing the strength and resilience of the final item. Non-destructive screening approaches such as ultrasonic screening, radiographic testing, and visual examination are generally used to recognize prospective problems like porosity.
Performing pre-weld and post-weld assessments is also critical in keeping high quality control standards. Pre-weld assessments involve validating the materials, tools settings, and cleanliness of the job area to stop contamination. Post-weld assessments, on the other hand, examine the final weld for any type of defects, consisting of porosity, and confirm that it fulfills specified criteria. Implementing a thorough quality control strategy that includes complete testing treatments and inspections is vital to reducing porosity problems and making certain the overall top quality of welded joints.
Verdict
Finally, porosity in welding can be a common problem that affects the top quality of welds. By recognizing the common sources of porosity and executing finest methods for avoidance, such as appropriate welding strategies and screening actions, welders can make certain premium quality and dependable welds. It is view website vital to focus on avoidance techniques to lessen the incident of porosity and preserve the stability of bonded structures.